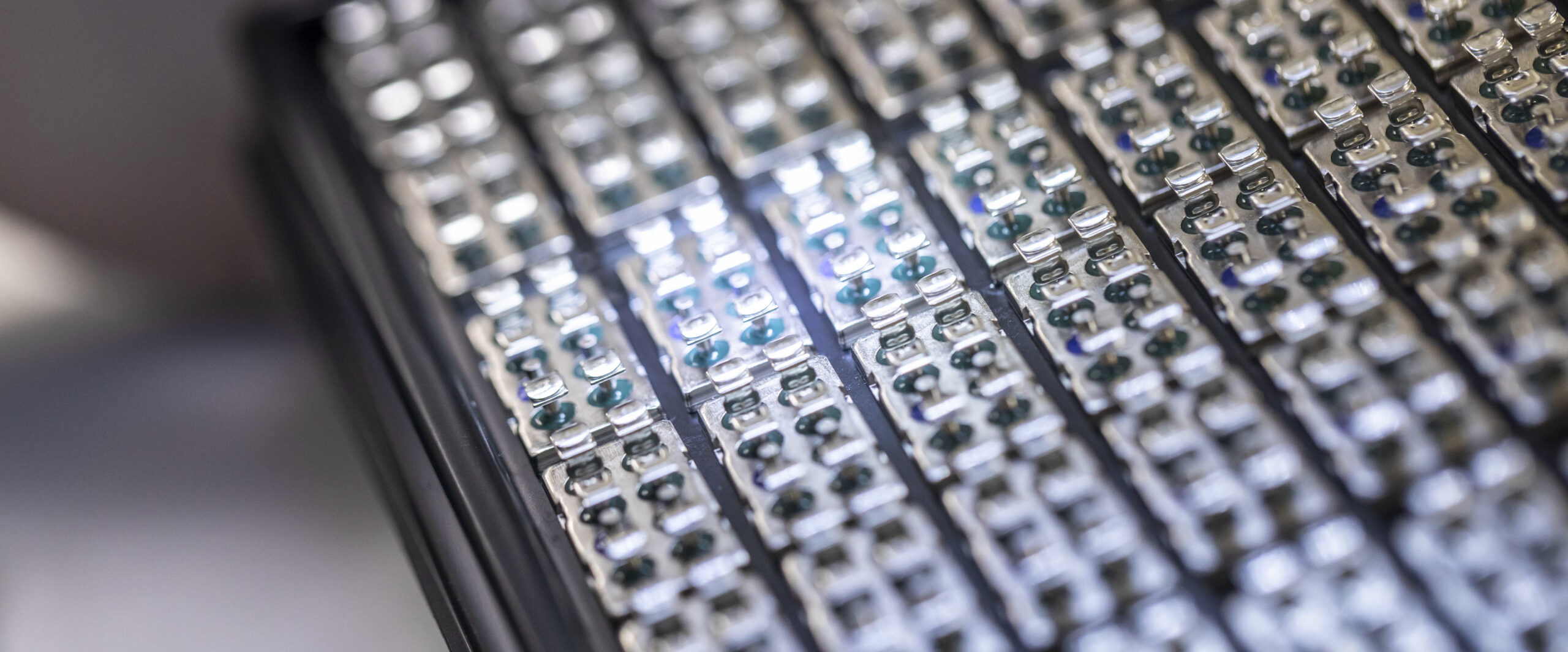
Behind the Scenes of Aerospace Advancements: Leach International’s Manufacturing Facility
Victor Hugo Melendez
Vice President of Operations,
Leach International Corporation
In the rapidly evolving aerospace industry, the need for increased production volume, reliability, and on-time delivery has become a major determinant in selecting suppliers. This is where Leach International’s manufacturing and assembly hub in Tijuana, Mexico, plays a role by providing a facility to manufacture quality, mission critical parts.
Cost-competitive manufacturing in Tijuana, Mexico
Covering over 71 thousand square feet for manufacturing, office and logistics, the Tijuana facility has been operational since 1980 and contains over 500 pieces of equipment crucial for manufacturing sub-assemblies of electrical switchgear and power distribution.
Over 400 staff focus on cost-effective manufacturing and intricate, sophisticated processes. These include meticulous piece parts manufacturing, sub-assemblies, annealing (heat treatment), plating, coil winding, soldering, and welding, ensuring every component meets exacting standards. Emphasizing vertical integration, the facility reduces reliance on third-party suppliers in order to keep strong control over quality, production timelines, and cost management.
The facility boasts 20 specialized production lines for various stages of manufacturing, from metal stamping to mechanical and final assembly, including multiple NADCAP-certified processes. The manufacturing area is complemented by warehousing, shipping, and administration, ensuring a seamless flow from production to delivery.
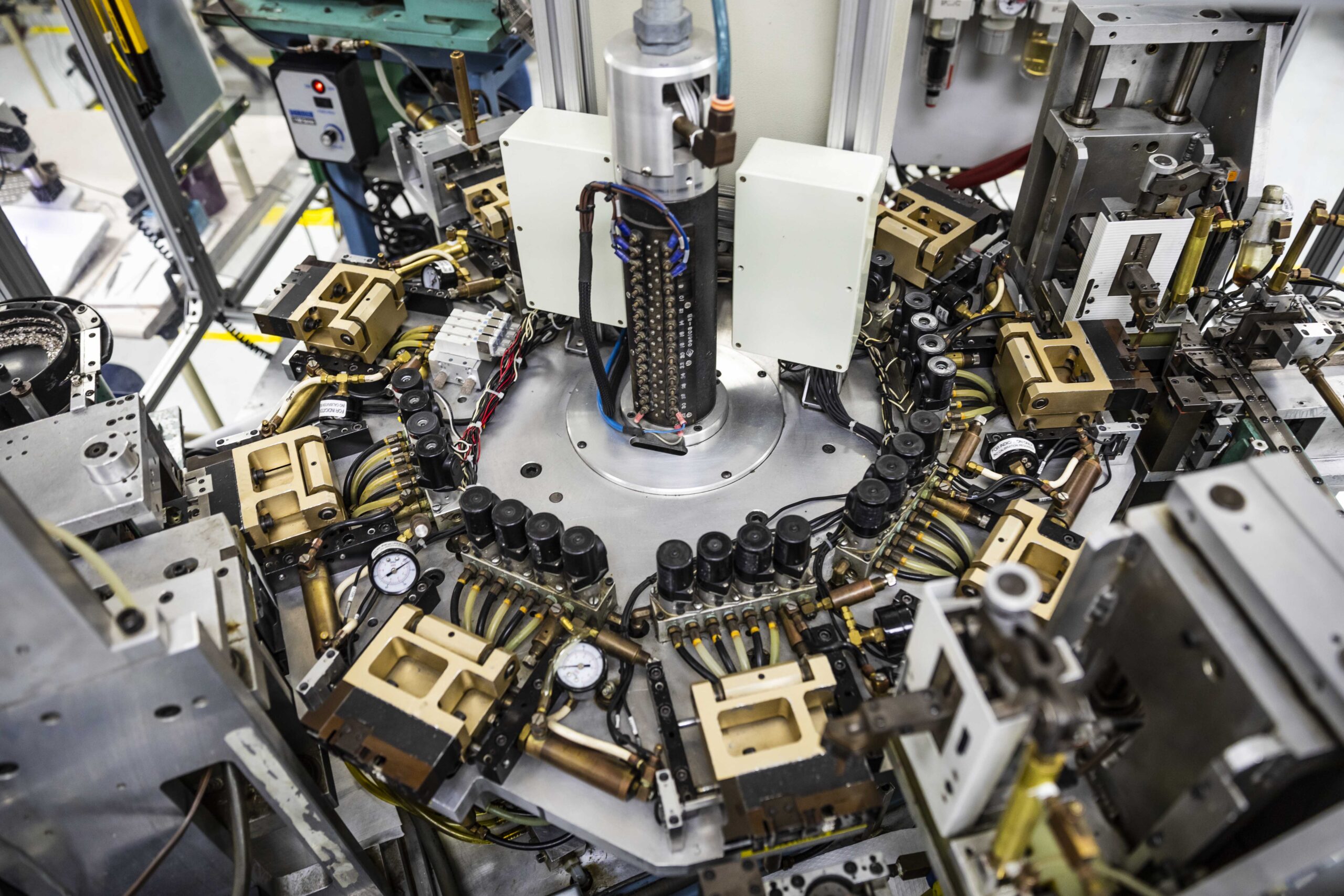
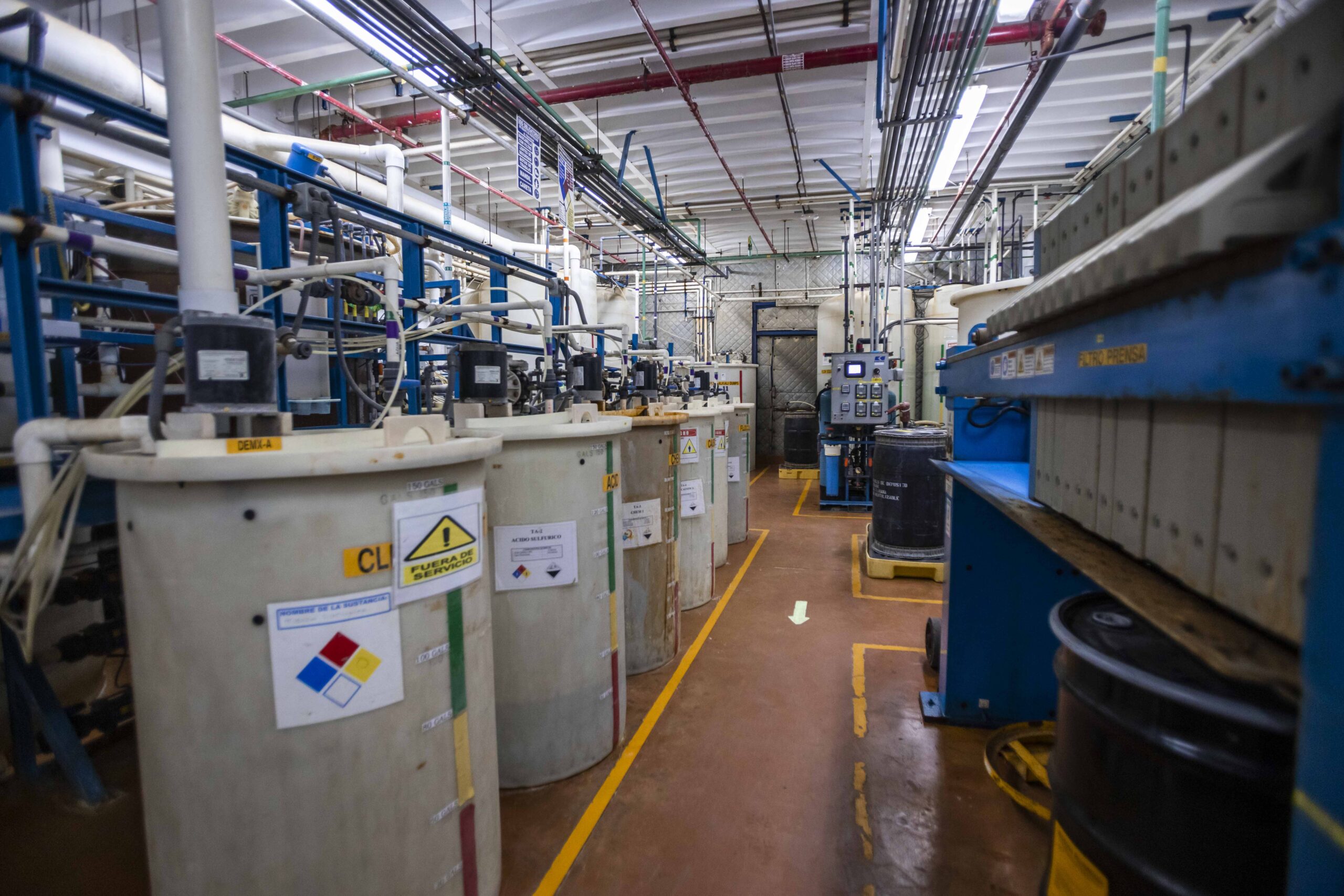
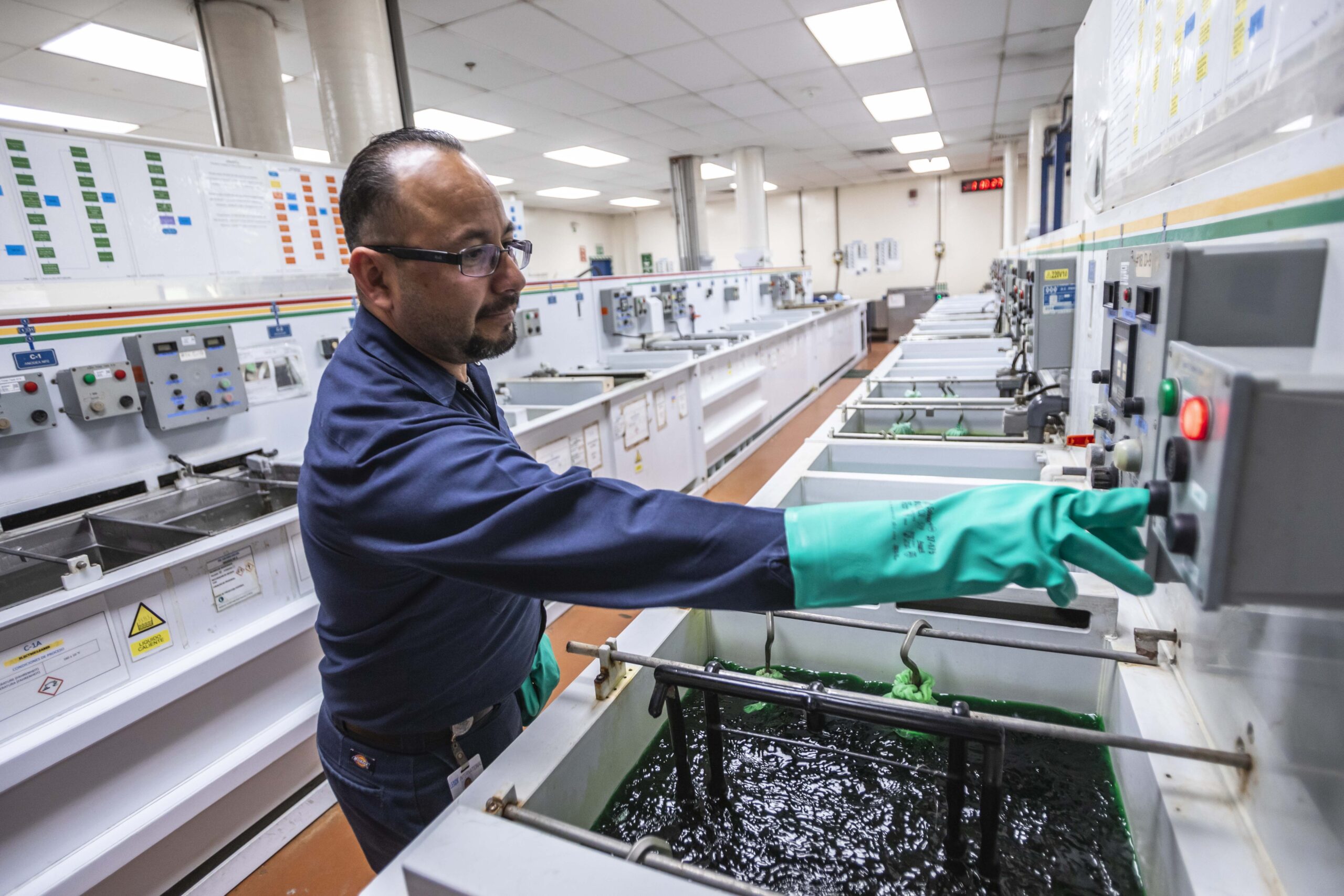
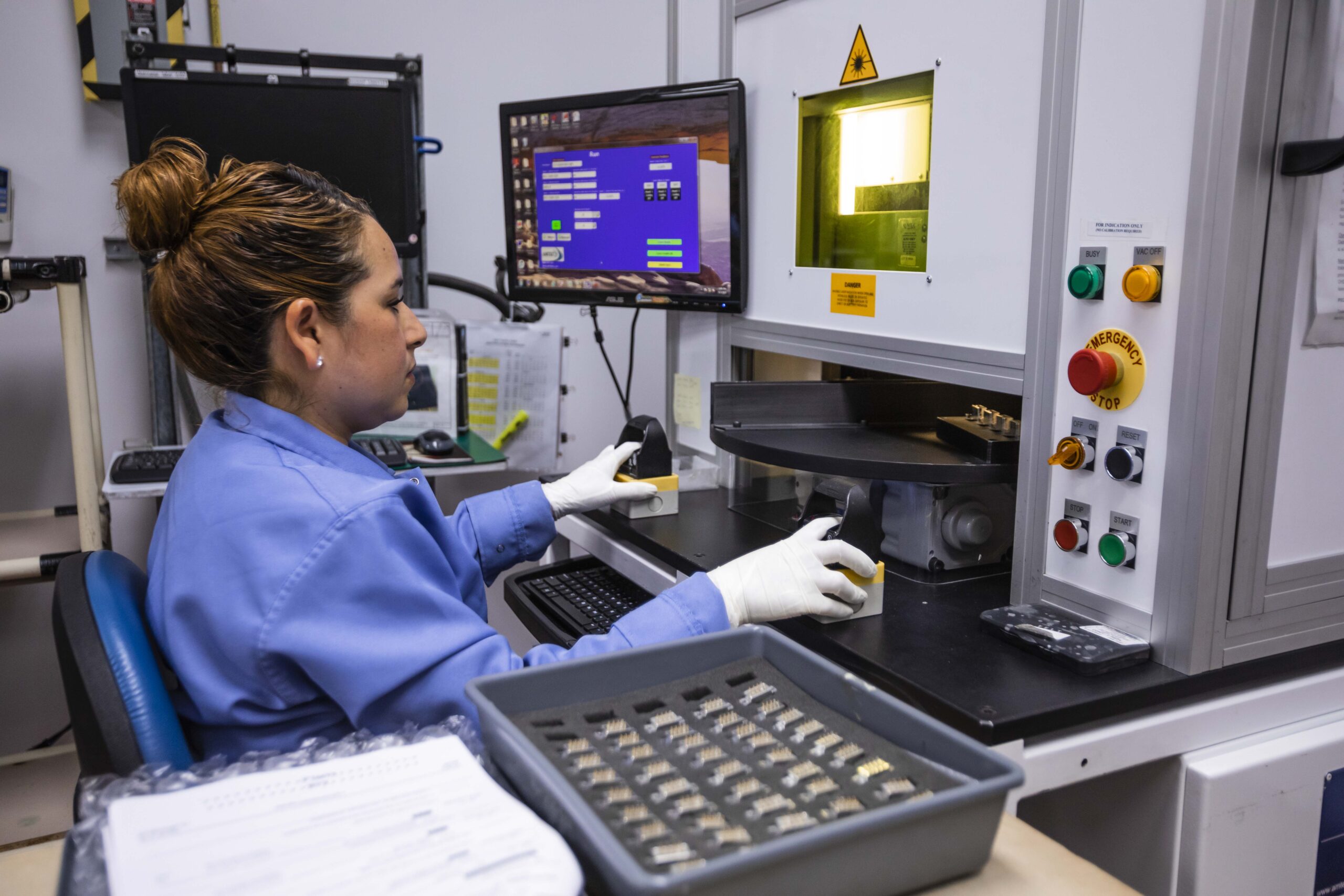
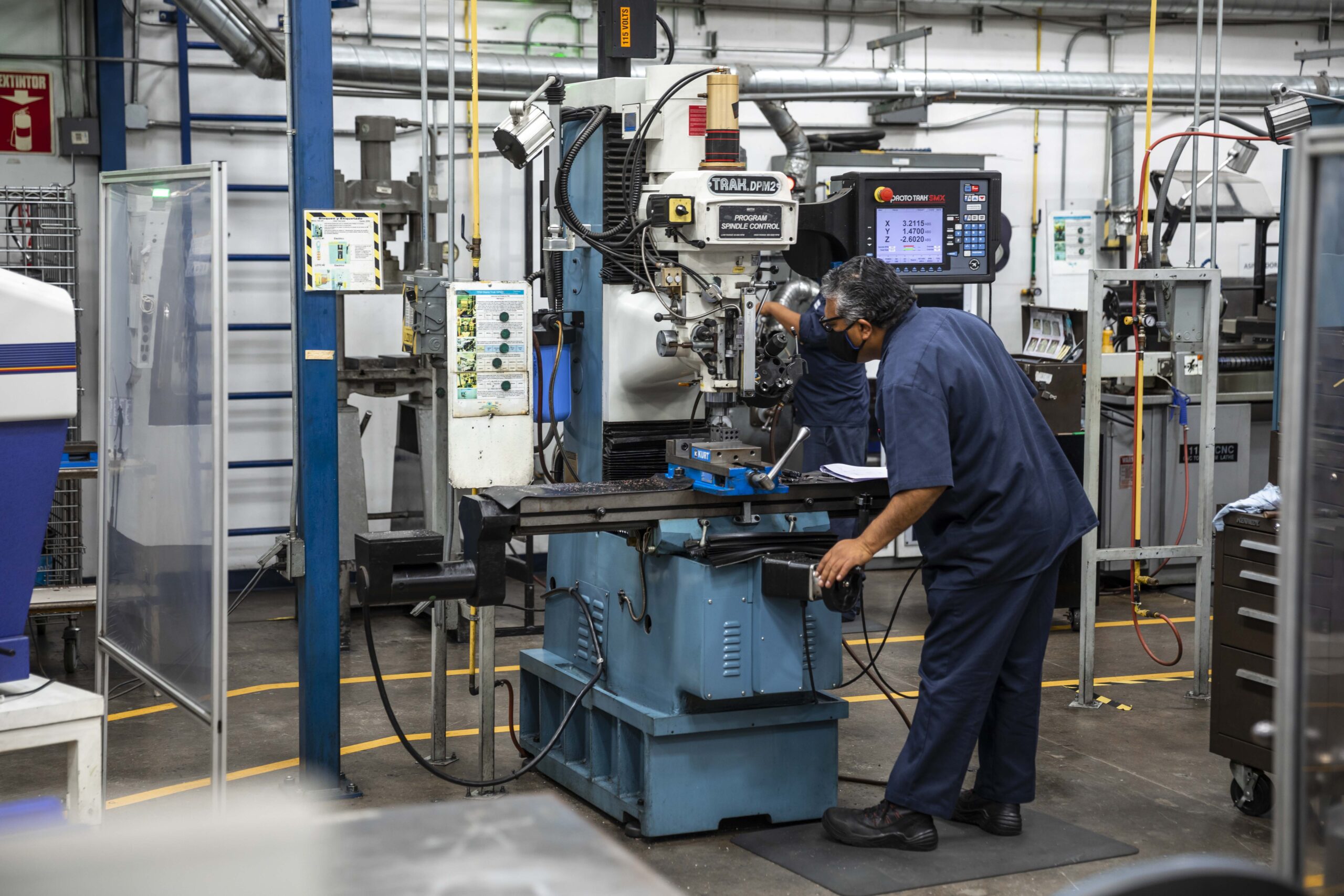
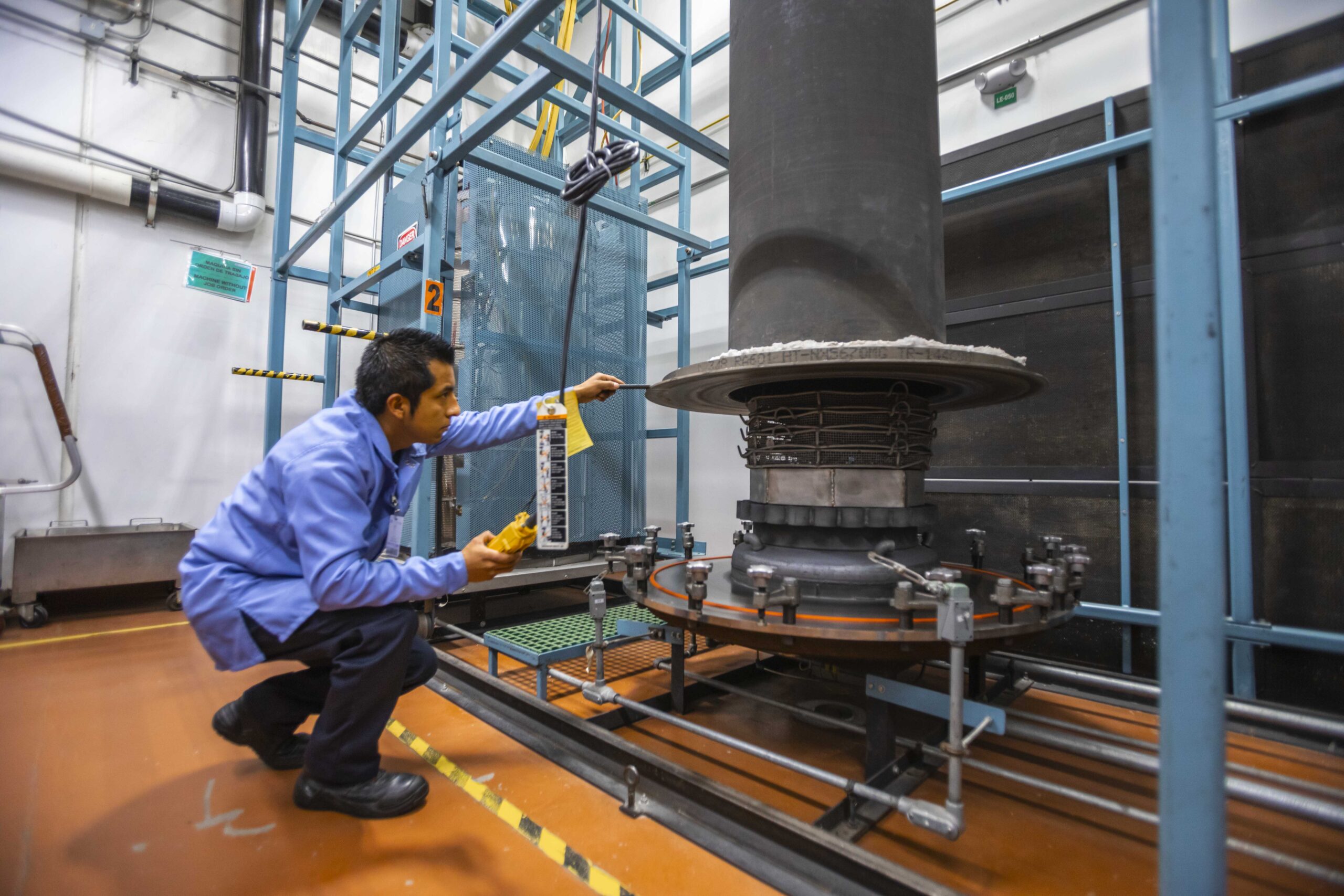
Complex processes support any power distribution need
Technical capabilities are marked by the use of advanced materials and manufacturing processes: The Fabrication/Coil/GMS departments produce over 800,000 various parts and sub-assemblies monthly, supporting the Relay Power Distribution Assembly (RPDA) and Contractor Control Device (CCD) Business Units.
The RPDA manufactures thousands of 5 Amp and 10 Amp relay units monthly, including the J-Series, K-Series, and X-Series, as well as tens of thousands of sub-assemblies to support the production of high-reliability and space-operation relays at our facilities in Buena Park. All of these products are essential in ensuring reliable power distribution and control of aircraft systems. The CCD team produces thousands of high-current switching contactors, including rotary contactors like the 9207-Series, non-latching balanced armature types like the HC-Series and solenoid types like the AJ-Series.
These highly reliable switchgears control the flow of electrical power, ensuring safe and efficient operation of an aircraft’s electrical systems, from landing gear to communication equipment.
Automated efficiency and scalability
The high production volume of Leach’s Tijuana facility is made possible by the facility’s capacity and efficiency, enhanced by automation. Sub-assembly automatic machines reduce the margin of error. The focus on continuous improvement and lean manufacturing methodologies create opportunities for new production lines to be added as necessary, with the addition of second and third shifts when customer demand requires this.
Equipment
In aerospace manufacturing, key challenges include maintaining high precision, ensuring component reliability under extreme conditions, and adapting to rapid technological advancements. Leach’s Tijuana facility addresses these with ongoing investment in state-of-the-art equipment:
- Glass to metal seal furnaces create hermetic seals between glass and metal components, essential to prevent air or moisture from infiltrating sensitive electrical components. These seals ensure the integrity of the hermeticity, critical in reliable operation of the switchgear in the harshest environments.
- Laser welding machines use high-energy lasers to precisely and cleanly fuse metal components in intricate electrical assemblies for aircraft. They ensure precision and maintain the structural integrity of these components, and their hermeticity, contributing to overall system reliability.
- Annealing furnaces heat materials to specific temperatures and then gradually cool them down, relieving stress and enhancing material properties. This process improves the ductility and mechanical properties of materials, essential for aerospace components exposed to critical conditions.
- Plating lines apply metallic coatings to components, providing corrosion resistance and ensuring proper electrical conductivity. Plating enhances the durability of electrical parts and helps maintain their electrical performance in challenging environments.
- Semi-automatic carrier machines are used in assembling the moving components crucial for the current switching process within relays. The semi-automatic machines streamline the assembly process, ensuring precision and consistency.
- Wire EDM (Electrical Discharge Machining) is a machining method that uses electrical discharges to shape or cut metal parts with exceptional precision, crucial for creating complex aerospace components that meet strict standards for fit and function.
- High VAC (vacuum) ovens create a controlled vacuum environment essential for removing contaminants, moisture, or volatile substances from components. This ensures components meet rigorous cleanliness requirements demanded by aerospace applications.
- Precision cleaning machines meticulously clean components to meet stringent standards. This ensures that electrical components are free from contaminants that could compromise their performance or longevity in critical systems.
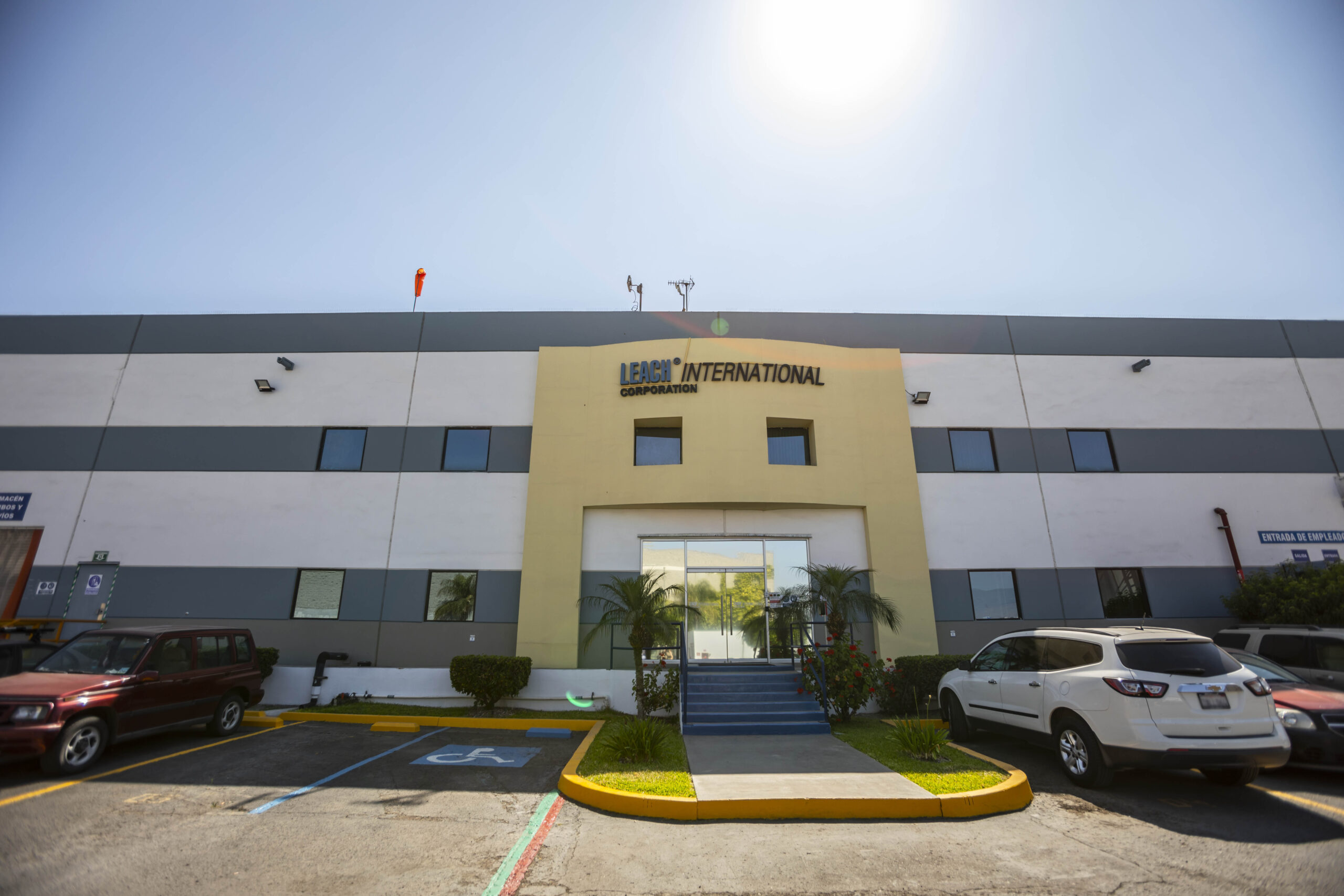
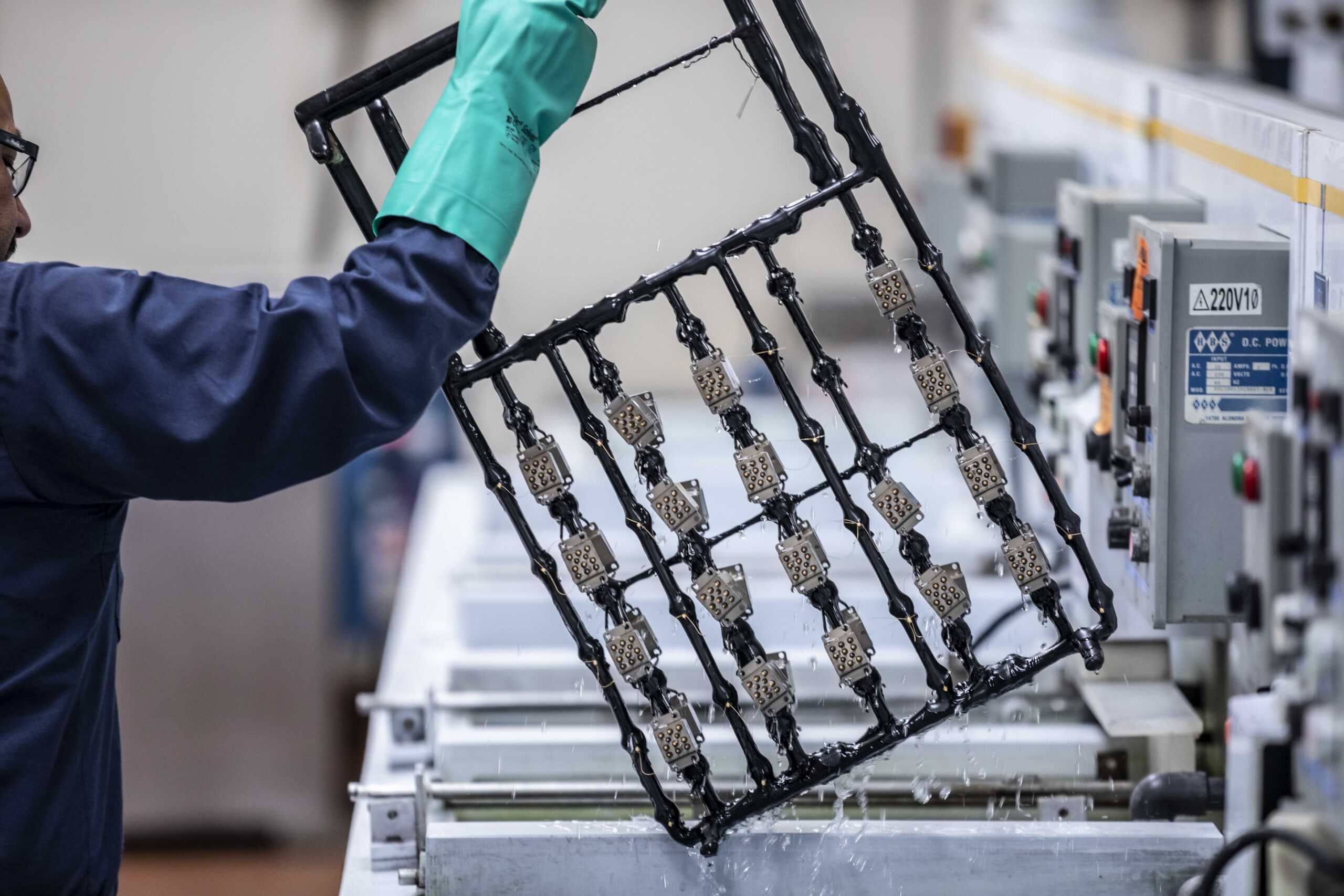
Excellence has quality at the core
Aerospace manufacturing is held to rigorous quality standards – reliability, safety and performance in demanding environments are non-negotiable. Standards that encompass various aspects of design, manufacturing, testing, and quality control are held high at Leach’s Tijuana facility, which boasts AS9100, ISO9001:2015, and MIL-STD-790 certifications, as well as NADCAP certification in chemical processes, heat treatment and welding.
—-
Leach’s Tijuana facility is a hub of advanced aerospace manufacturing, equipped with the latest technology and machinery. Here, we’re continually predicting and adapting to the complexities and requirements of modern aerospace engineering, integrating technology and industry knowledge to meet evolving demands.
Contact relayed@leachcorp.com if you would like to find out more about Leach manufacturing.
Victor Hugo Melendez Engineering Solutions with Global Impact
Vice President of Operations, Leach International Corporation
As VP of Operations, Victor brings 20 years of industry expertise, underpinned by his Bachelor’s degree in Applied Mathematics and Master’s in Industrial Engineering. His proficiency in global manufacturing and quality systems management is complemented by his Six Sigma Black Belt.
Victor’s international experience and passion for soccer mirror his dynamic approach to manufacturing leadership.