Charging Ahead: Power Demands and Challenges in an MEA Era
Hassan Dar
Electrical Design Engineer
The aerospace industry is fast moving towards a more electric future, bringing a surge in power demands and a new set of high-altitude challenges. Driven by the urgent need to decarbonize flight and reduce environmental impact, the challenge is to integrate novel fuel types and disruptive technologies, such as hybrid-electric propulsion systems.
Hybrid-electric aircraft have the potential to change the aviation landscape by enhancing energy efficiency and significantly reducing CO2 emissions. For commercial jets, this technology could decrease emissions by up to 5%, while for helicopters, the reduction could reach an impressive 10% due to their lighter weight. However, the transition to hybrid and fully electric aircraft introduces a new set of challenges, particularly in power management.
A surge in power demand
The transition to MEA technology has led to an exponential rise in the electrical power required onboard. Future hybrid and electric aircraft will require megawatts of power to operate, necessitating substantial improvements in power electronics. The integration of electric actuators, flight control systems, and the potential for electric propulsion promise enhanced efficiency and reduced reliance on hydraulic and pneumatic systems. These advancements must address the integration, performance, efficiency, and component size and weight of power electronics to meet the stringent demands of the aerospace industry, and face a key challenge: Increased electrification results in heavier power loads and the need for advanced power distribution and management systems.
Advances in battery technology are equally important for the aerospace industry’s transition to more electric and hybrid-electric aircraft. The development of batteries with higher energy densities and faster charging capabilities is essential to extend the range and efficiency of electric aircraft. Innovations in lithium-sulfur and solid-state batteries promise significant improvements such as greater energy storage and better safety profiles compared to traditional lithium-ion batteries.
Safety first
With higher operating voltages comes the heightened risk of electrical arcing and other safety hazards, particularly at high altitudes where the air is less conductive. Ensuring the safety of these complex electrical systems is paramount. Advanced circuit protection and fault management systems are essential to mitigate these risks. For military applications, the stakes are even higher. The development of Megawatt Tactical Aircraft and Next Generation Air Dominance (NGAD) fighters requires power control solutions that can handle the inrush current of highly capacitive loads without compromising performance or safety.
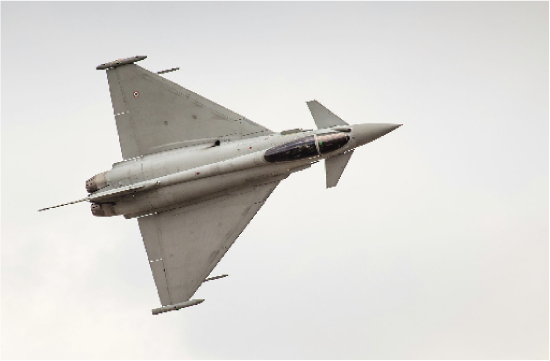
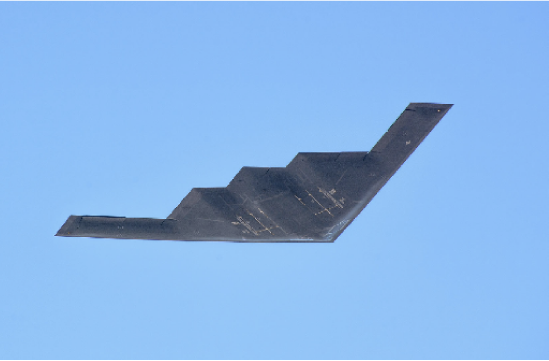
The quest for sustainability
In addition to slashing CO2 emissions, hybrid-electric and all-electric propulsion systems play a vital role in meeting broader environmental objectives. They offer a quieter alternative to conventional engines, significantly reducing noise pollution – a major concern around airports and densely populated flight paths. These technologies open the door to using renewable energy sources for charging, further decreasing the aviation industry’s carbon footprint.
Solid state innovations
Solid-state technology is changing the way we manage power in aerospace. It’s replacing traditional mechanical components with semiconductor devices, offering faster response times, greater reliability, and improved control over power distribution. Solid state power controllers (SSPCs) are at the forefront of this technological shift.
SSPCs provide precise control and protection for electrical systems, handling higher power densities and offering advanced features such as programmability and real-time monitoring. They use solid-state switches, such as Silicon Carbide (SiC) MOSFETs, which are capable of fast switching speeds and high efficiency. These switches are managed by microcontrollers that enable precise operations, circuit protection, fault detection, and communication interfaces. With comprehensive protection mechanisms, SSPCs safeguard against over-current, over-voltage, and over-temperature conditions.
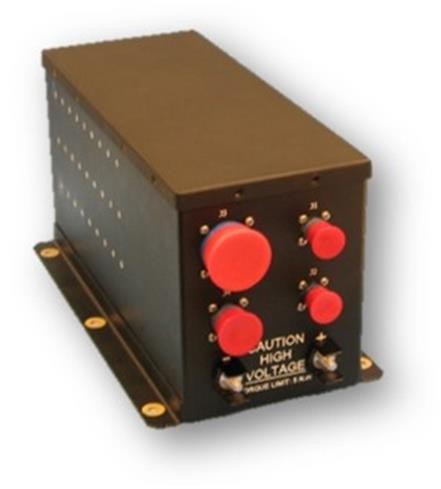
Managing power with 270 Vdc SSPCs
Leach Corp’s 270 VDC SSPCs are engineered to meet the rigorous demands of modern aerospace electrical systems. They are designed to manage the inrush current associated with highly capacitive loads, a critical requirement for both commercial and military aircraft. Using SiC MOSFETs offers several advantages over traditional silicon-based MOSFETs, including higher breakdown voltage and lower on-resistance. This results in reduced power dissipation and fewer MOSFETs required in parallel operations for high current applications. The ability to distinguish between capacitive load inrush and a sustaining short circuit event is a patented feature that prevents nuisance trips, ensuring continuous power delivery to healthy loads.
Leach Corp’s scalable and modular SSPCs allow for customization based on specific application requirements. They feature efficient heat dissipation designs and comply with stringent certification standards, ensuring reliable operation under demanding conditions
Hybrid contactors for higher power levels
In addition to the important role of SSPCs in the evolution of aerospace power management, hybrid contactors represent a significant leap forward in switching technology at higher power levels. Leach Corp’s 270 VDC hybrid contactor has a remarkable switching capacity of 50,000 cycles. This far surpasses that of conventional 270 VDC contactors, especially those rated above 200 amps, which typically offer less than 10,000 cycles. By merging an electromechanical contactor with a solid-state switch, this hybrid contactor minimizes the wear and tear from arcing during the switching process.
This patented technology extends the life of the contactor and significantly cuts down on total lifecycle costs, making it a good choice for high-reliability applications in both military and commercial sectors.
Looking ahead
The future of power management in aerospace is closely tied to the advancement of solid-state technology and the push for sustainability. As aircraft systems become more electric, the need for efficient, reliable power control becomes increasingly critical. SSPCs will play a vital role in managing the complex electrical loads of next-generation aircraft. The demand for higher operating voltages in aircraft electrification is leading to developments beyond 270 Vdc, potentially exceeding 1000 Vdc, and advancements in SiC MOSFET technology are expected to further improve SSPC performance and capabilities, contributing to safer, more sustainable flight.
To learn more about Leach Corp’s SSPC portfolio, visit our website.

Hassan Dar – Experienced Engineer
Contactors & Control Devices Business Unit Engineering Lead, Leach International Corporation
Hassan Dar, CCD Business Unit Engineering Lead, is an Electrical Engineering graduate from the University of California, Los Angeles. With extensive expertise in PCB, circuit design, and project engineering, Hassan has significantly contributed to the development and testing of PCBs, ensuring they meet both customer and environmental standards. His work includes the successful design of Ideal Diodes and Motherboards for Skywalker’s HV PDA and DC PDA systems, and a role in transitioning prototypes to production-ready safety units.
Hassan’s ability to seamlessly coordinate project timelines and liaise with customers to overcome design challenges underscore his technical prowess.