Design & Manufacturing Expertise

Leach International has been synonymous with design excellence and reliability in power distribution solutions since 1919. Our cutting-edge components and systems are integral to thousands of aerospace, defense, rail, and high-end industrial applications worldwide, ensuring performance in mission-critical environments.
We are recognized as the industry leader in power distribution, combining advanced components with unique design and manufacturing capabilities to deliver custom AC/DC power distribution assemblies. These include primary and secondary power distribution units, relay and central warning panels, GFI units, thrust reverser control units, ELCUs, smart contactors, wiring integrated assemblies, windshield anti-ice controllers, and other electronic switchgear.
Design: Ready for Installation & Customized Solutions
Our extensive product catalog features thousands of pre-certified solutions ready for immediate installation. Additionally, our capabilities extend far beyond what is listed. If you need a custom electrical solution, our expert engineers are ready to assist. Our design team can develop custom solutions to meet specific needs that may not be addressed by our standard offerings.
Previous platforms using our custom solutions include Embraer E2, Airbus, Comac, Military ground vehicles, Boeing 737, Boeing 747, Boeing 777, Hubble Telescope, Curiosity Mars Rover, F-16 Falcon, and F-22 Raptor. Each custom solution receives a unique part number specific to its design.
Whether you require a unique part or assembly, we’re committed to delivering high-quality, reliable solutions that meet the most demanding requirements.
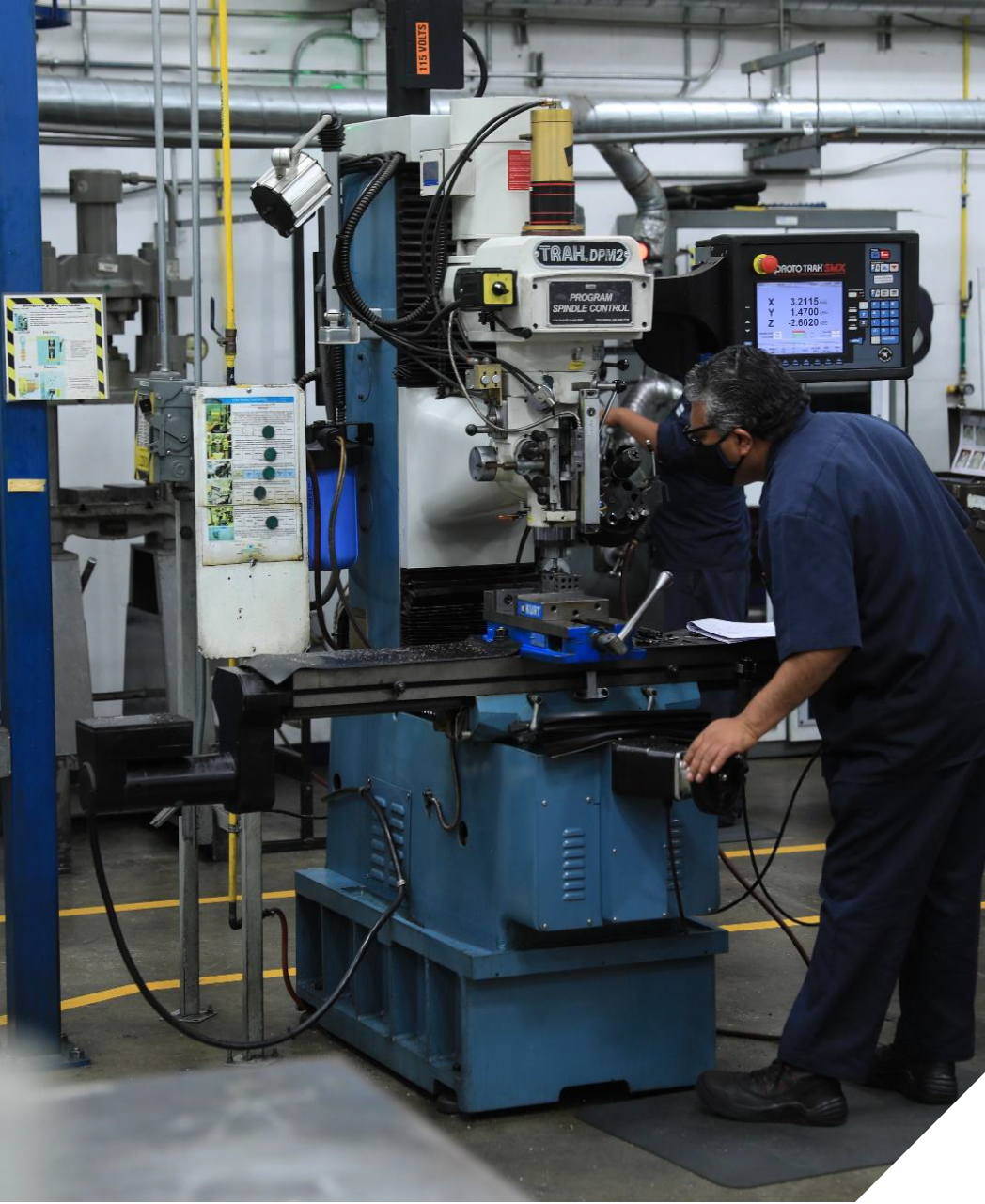
Cost-Competitive Manufacturing
Our manufacturing facilities have nearly 200,000 square feet of space, filled with over 500 pieces of capital equipment essential for producing electrical switchgear and power distribution assemblies. With a team of over 400 dedicated staff, we focus on cost-effective, intricate processes, including piece parts manufacturing, sub-assemblies, annealing, plating, coil winding, soldering, and welding.
Our emphasis on vertical integration minimizes reliance on third-party suppliers, ensuring strict control over quality, production timelines, and costs. Our facility features 20 specialized production lines for various manufacturing stages, from metal stamping to final assembly, including multiple NADCAP-certified processes.
Custom manufacturing services
Power Distribution Assemblies:
- Relay and central warning panels
- Ground fault interrupter (GFI) units
- Thrust reverser control units
- Electrical load control units (ELCUs)
- Smart contactors
Additional Custom Solutions:
- Wiring integrated assemblies
- Windshield anti-ice controllers
- Weapons release boxes
- General electrical equipment
- Custom current level power contactors
- Custom design requirements
Testing Meets and Exceeds Expectations
Standards that encompass various aspects of design, manufacturing, testing, and quality control are held high at our manufacturing facility, which boasts AS9100, ISO9001:2015, and MIL-STD-790 certifications, as well as NADCAP certification in chemical processes, heat treatment and welding.
Rigorous in-house testing meets or exceeds MIL-spec standards:
- ✓ Testing capable of MIL-PRF-83536, MIL-PRF-6106, MIL-PRF-83726. RTCA DO160 and Mil-std-810, RTCA DO-178.
- ✓ We can provide design and testing to DO-160 and custom levels.
- ✓ Mixed load and low level (<25A rated relays) available.
Types of testing:
- Internal moisture
- Intermediate current
- Thermal shock
- Most QPL relays are tested @ 200Gs
- Can go as high as 1500 Gs (High Reliability)
- Sine/Random vibration
- Terminal strength
- Overload (AC/DC)
- Mechanical life test: Rupture test – 4,000 Amps @ 28 VDC & 2,500 Amps @ 115 VAC, 400 Hz
- Resistance to solder heat
- Time current relay characteristics: Continuous current test – up to 80,000 ft @ +125oC and rated current
Contact Our Engineering Experts
CONTACT OUR ENGINEERING TEAM.
CALL (714) 736-7598