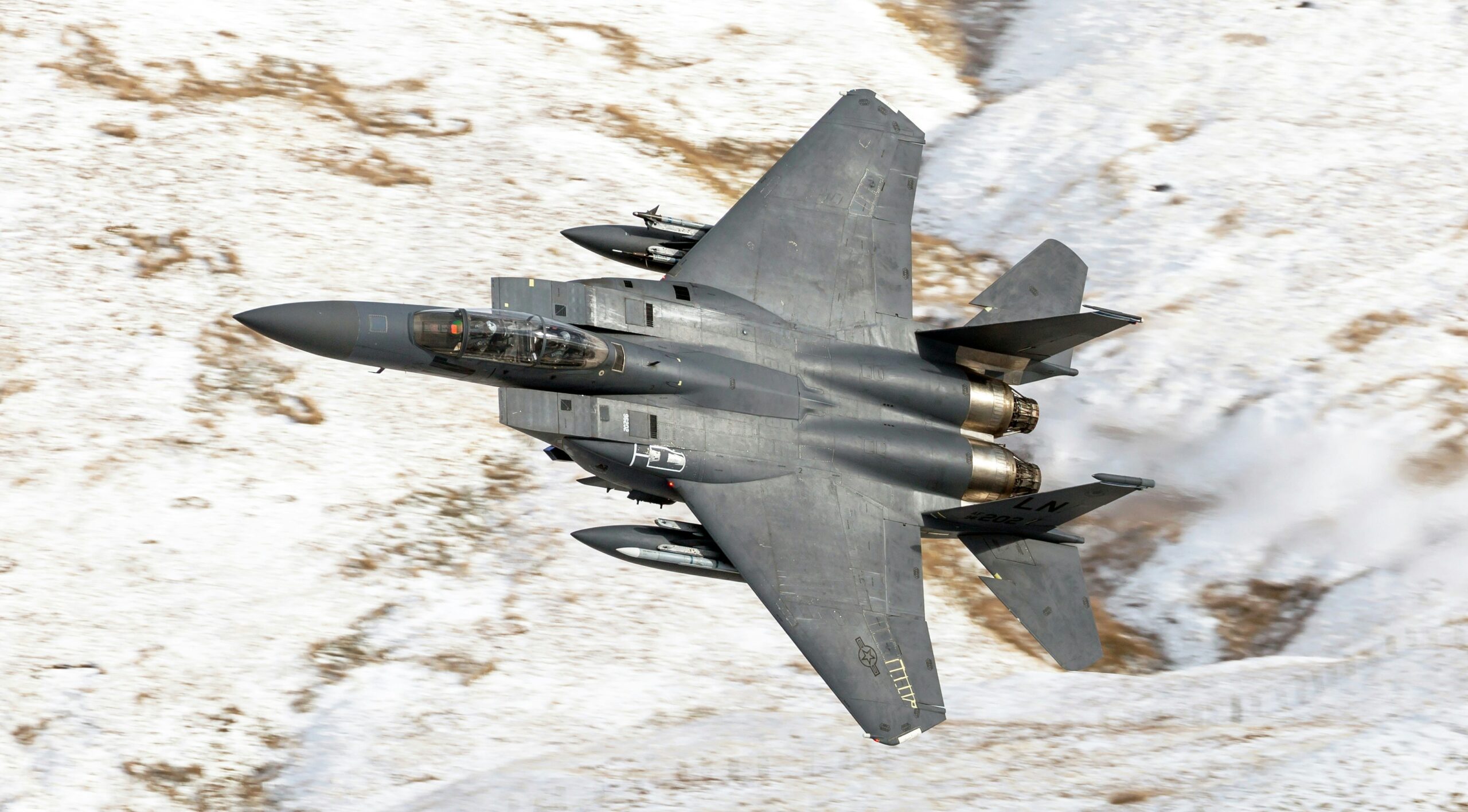
Sky-High Power:
The Evolution of Aircraft Electrical Systems
Jackson Clark
Business Unit Manager for Relays and Power Distribution Assemblies,
Leach International Corporation
Beginning with the rudimentary electrical components of the early Wright Flyer, advancements in aircraft electrical systems have been relentless, evolving from simple wiring for basic communication and ignition to complex networks capable of managing a diverse array of onboard electrical needs. This journey has been driven by the demands of increasing air traffic, performance optimization, and the need for more efficient and cost-effective operations.
When the Wright Flyer took to the skies in the early 20th century, electrical systems were no more than basic wiring and components. These were for powering communication and ignition systems, with early DC generators typically rated below 500 W. But the introduction of lighting, signaling, and heating systems during the interwar period required more robust power generation. The shift from 6 VDC to 28 VDC systems by 1936 marked a significant leap in power capacity, accommodating a growing array of onboard electrical needs.
Post-World War II, the aviation industry witnessed a shift towards AC generation systems, driven by the need for higher power density and reliability. There were significant improvements in AC generators, which were lighter and smaller compared to their DC counterparts, offering higher operating voltages and improved maintenance and lifetime performance. However, these advancements also brought new challenges, such as managing reactive power and selecting appropriate frequencies for operation.
More-Electric Aircraft – A Paradigm Shift
More-Electric Aircraft (MEA) use electrical power to drive non-propulsive aircraft systems, with the goals of optimizing aircraft performance and decreasing operating and maintenance costs. It is a significant paradigm shift, with a focus on replacing mechanical, hydraulic, and pneumatic systems with electrically powered alternatives.
In aircrafts like the Airbus A380 (commercially released in 2007) and the Boeing 787 (2011), there were substantial increases in onboard electric power demand. These aircraft, characterized by intensive electrification, implemented Variable Frequency Generators directly coupled to engines, replacing traditional Integrated Drive Generators. The Boeing 787, for instance, uses four 250 KVA VFGs and the Airbus A380 employs four 150KVA VFGs. The move to a bleed-less architecture in these aircraft, where high-pressure air is not extracted from the engines for secondary systems, created more efficient engine operations and thrust production. A key prize was the considerable reduction in operating costs: The Boeing 787 achieved about a 14% reduction in block hour operating costs compared to its predecessor, the Boeing 767.
What’s next? The Role of Solid-State Power Controllers
The MEA continues apace as the aerospace industry looks for increasingly sophisticated electrical systems. These are poised to take over areas such as actuation, fuel handling, and cabin air pressurization. Looking ahead, there’s a striking prospect of distributed and electrically powered propulsion, in line with the industry’s sustainability goals. Currently, onboard electrical power generation capacity in new aircraft models is reaching impressive heights, with figures around 1.5 MVA. Forecasts suggest this trend will intensify. Consequently, aggressive power density targets are being established for the next generation of electric generators and power electronic equipment. These innovations are not just redesigning aircraft systems; they are redefining the very essence of flight for a greener, more efficient future.
Solid-State Power Controllers (SSPCs) are key components in managing the complex electrical distribution required in MEAs. Their ability to handle intricate power distribution algorithms and rapid fault detection is essential for advanced electrical systems.
Leach’s range of SSPC options play an important role in realizing the vision of MEA and addressing the future electric power needs of the aerospace industry, offering numerous benefits: Enhanced reliability, precise control, and faster response times compared to traditional electromechanical systems. These devices are adept at handling complex power management tasks, crucial for the sophisticated electrical systems of MEAs. Their technical characteristics, such as rapid fault detection and interruption, high-current handling capabilities, and compatibility with high-voltage systems like Lithium-Ion batteries, make them integral to the safe and efficient operation of next-generation aircraft.
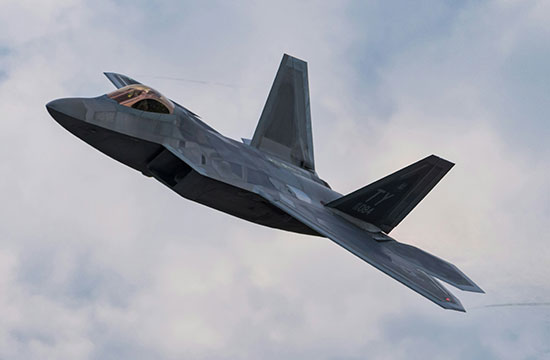
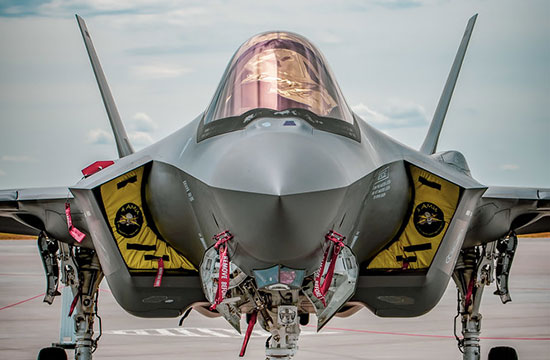
270 VDC SSPCs
Leach’s 270 VDC SSPCs are designed for high-power applications needed in the transition towards more sophisticated and environmentally friendly aircraft systems. Utilizing Silicon Carbide (SiC) MOSFETs, they can withstand higher voltage levels and offer higher thermal performance and characteristics. Their resilience to extreme stresses caused by pulsed transient operations in high-power switching applications is particularly important in modern aircraft, where power efficiency and switch reliability are paramount.
These SSPCs are engineered to adeptly handle challenges posed by high-voltage systems, such as those involving Lithium-Ion batteries. These batteries, while providing substantial power, can deliver significant fault currents during short-circuit conditions. Leach’s SSPCs are designed to respond swiftly in such scenarios, ensuring the safety and integrity of both the electrical system and the battery. Their ability to manage inrush current, differentiate between high inrush currents and dangerous short circuits, and handle the regenerative energy of inductive loads, sets them apart. Features like voltage clamps, insulated metal substrate for thermal management, and safety crowbar interlocks, underscore the comprehensive approach to safety.
As the aviation industry continues to evolve towards MEA and seeks more efficient and sustainable solutions, Leach’s 270 VDC SSPCs are becoming a critical component of this transformation. Their robust design, coupled with Leach’s commitment to quality and adherence to rigorous certification standards, make them a significant contribution to the future of aerospace power management.

Jakson Clark
Business Unit Manager for Relays and Power Distribution Assemblies
Renowned for his meticulous, data-driven approach, Jakson Clark brings a decade’s experience in aerospace and medical devices to Leach. His expertise in engineering and management is fortified by an MBA and Bioengineering degree from Oregon State University and a Project Management Professional (PMP) certification.