When Failure is Not an Option
Canh Tran
Principal Manufacturing Engineer
Understanding Mission-Critical Applications in Modern Aerospace
The term “mission critical” refers to systems and components where failure cannot be tolerated, those essential to safe aircraft operation. Mission-critical systems undergo rigorous certification processes with specific requirements for redundancy, fault tolerance, and environmental resilience. From primary flight controls to essential power systems, the components are subject to meticulous testing regimes, comprehensive maintenance schedules, and exacting reliability metrics that exceed those of standard equipment
Power distribution architecture
Power is responsible for managing and distributing electrical energy from generation sources to various systems and subsystems. It ensures that essential functions such as avionics, flight controls, lighting, and environmental systems receive uninterrupted power, even under demanding conditions. Advanced designs prioritize efficiency, reliability, and safety while minimizing weight and space. Distributed architectures, for example, reduce cable weight and improve redundancy by segmenting power management into zones.
Leach offers the aviation and aerospace industry the most comprehensive catalog of power distribution solutions, manufacturing custom AC/DC power distribution assemblies that incorporate advanced features, such as built-in test capabilities (PBIT, CBIT, IBIT) and precise overcurrent protection with thermal memory. Solutions include primary and secondary power distribution units, relays, smart contactors, and central warning panels. Leach is also at the forefront of next-generation high-voltage systems for electrified aircraft, ensuring lighter, more efficient designs that meet everincreasing power demands.
Any aircraft we board today contains hundreds of mission-critical components, many of which are designed and produced by Leach International. Core mission-critical systems that must be responsive immediately and flawlessly, even in the most extreme operating conditions, include flight control and engine management systems.
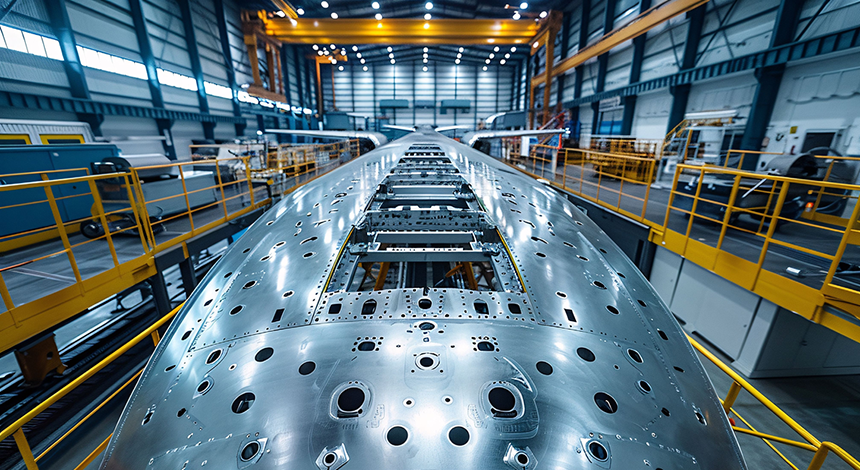
Flight control systems
Flight control systems maintain stability, maneuverability, and safety during all phases of flight. They enable pilots to control the aircraft’s altitude, speed, and trajectory, ensuring smooth operations from takeoff to landing. Modern flight control systems combine precision engineering with built-in test capabilities. They’ve evolved from mechanical linkages to advanced fly-by-wire (FBW) technologies that rely on electronic signals and sophisticated algorithms to enhance reliability, reduce weight, and improve performance. Leach supplies power distribution units optimized for flight-critical operations and integrates “design-to-safety” electronics with programmable protection features – overcurrent protection, thermal memory, and fail-safe functions.
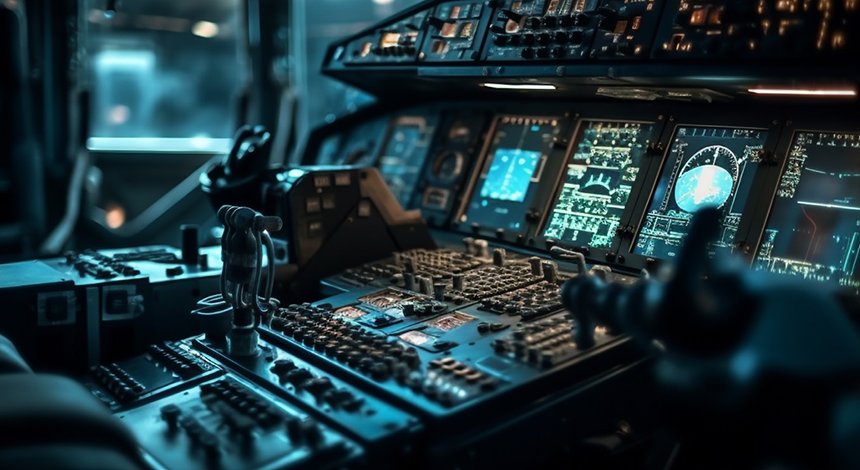
Engine management
Engine management systems ensure optimal performance, fuel efficiency, and safety, as they control and monitor various engine parameters – fuel flow, ignition timing, and thrust levels – to maintain reliability under all conditions. Advanced digital systems, like Full Authority Digital Engine Control (FADEC), provide precise adjustments and fault detection, enabling real-time responses to potential issues while reducing pilot workload. Leach’s contactors and relays are designed for engine control applications and to ensure seamless switching and fault protection under extreme conditions. While engine and flight controls get the attention, other equally important mission-critical systems
are at work:
• Leach’s thrust reversers prove critical during landings, especially on wet or short runways.
• Our Ground Fault Interrupters detect electrical problems in milliseconds – essential when those
problems could ignite fuel vapors. Boeing made these standards on 737s for good reason.
• Environmental control systems maintain proper cabin pressure and cool sensitive avionics.
When pilots face emergencies, our Solid State Power Controllers instantly reroute electricity to the
systems that matter most.
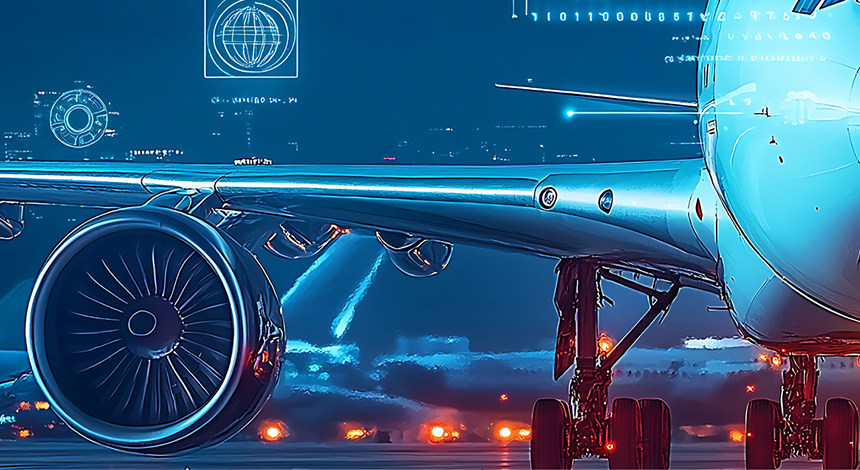
How these systems work together
Mission-critical systems rely on sophisticated networks balancing power, data, and load dynamics. This involves seamless coordination between hardware, software, and adaptive controls, often backed by Leach components. Integrated power-management centers dynamically allocate electricity based on real-time input from engines, flight controls, and cabin systems. Here, Leach’s intelligent power distribution units ensure critical systems like flight controls receive priority during emergencies, while less-essential systems such as galley equipment are reduced or disconnected. Digital networks are the aircraft’s nervous system, connecting automated load management with flight controls and engine systems. When cargo shifts during flight, for example, these networks trigger trim adjustments to maintain optimal center of gravity and fuel efficiency. Leach’s Remote Data Concentrators streamline these processes by gathering sensor data and reducing complex wiring, resulting in faster system responses. During takeoff, hybrid-electric aircraft power systems prioritize engine thrust while load management systems ensure proper balance.
If a generator fails, backup circuits immediately reroute power while alerting pilots to make necessary flight control adjustments. These interconnected systems ensure that critical operations continue uninterrupted.
Engineering for zero failure
When a relay controls critical aircraft electrical systems at 40,000 feet, its origin and testing history matter. Military Specifications (MIL-SPECs) ensure critical equipment functions reliably in extreme conditions – from Arctic cold to desert heat, from lightning strikes to severe vibration.
Leach’s components endure brutal MIL-SPEC testing. Our components face thermal cycling, shock simulations, and accelerated life tests that push them far beyond normal operating conditions. Each component undergoes First Article Inspection before production begins, and our AS 9100- and ISO 9001-certified manufacturing ensures complete traceability. Our relays comply with MIL-PRF-6106 and MIL-PRF-83536 for subminiature applications, requiring 100% screening for defects like contact resistance drift.
We build redundancy (multiple backup systems) into critical components. Dual data buses ensure that communication continues if one fails. Backup power systems activate if primary sources falter. Multiple protection layers catch cascading faults before they spread. Aircraft like the C-130J and Global Express incorporate these principles so that there’s no room for single points of failure.
Leach ensures uninterrupted electrical power through a trifecta of reliability, proactive monitoring, and redundancy. Our electromechanical switchgear has a proven track record across platforms like the Boeing 737 and F-22 Raptor, and many more commercial and military aircraft, with components engineered to endure extreme conditions while maintaining galvanic isolation for fail-safe operation. Built-In Test Equipment (BITE), such as Power-On, Continuous, and Initiated BIT (PBIT, CBIT, IBIT), perform real-time diagnostics to detect faults like ground faults in under eight milliseconds, preventing cascading failures. For redundancy, Leach integrates Solid State Power Controllers (SSPCs) and dual redundant data buses into power distribution systems, ensuring backup pathways during emergencies – a design validated in platforms like the Lockheed C-130J and Bombardier Global Express.
These layered safeguards, combined with field-proven performance across military, commercial, and rotorcraft applications, underscore Leach’s role in minimizing downtime and maximizing safety in mission-critical aviation systems.

Canh Tran
Principal Manufacturing Engineer
Canh Tran brings 47 years of aerospace manufacturing expertise to his role as Principal Manufacturing Engineer at Leach Corp. Since 1977, he has advanced through multiple engineering positions, specializing in relay design development and manufacturing process optimization. Canh has led engineering teams and spearheaded key projects, including the development of compact relays for space applications.